The beverage can washer has been an essential part of 2-piece beverage and food can manufacturing since the early 1960’s. Many innovations have taken place since the days when aluminum beverage cans were made from soaped aluminum slugs, and can washers used kerosene to clean them. Now, as well as in the very early days when “high speed” lines ran an amazing 125 cans per minute, a washer is positioned between the body makers and the decorator.
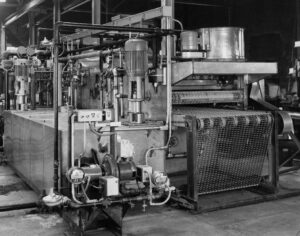
The can washer was then considered as just a necessary evil that was needed to clean up the body maker’s oily process such that the cans could be decorated and sprayed inside. Today, a washer is so much more.
The many features and operations of the modern can washer should be considered as a “value add” in the can manufacturing process.
The Process and the Value:
The process to clean, treat and dry a beverage can is as follows:
Pre-Rinse:
The cans are loaded in mass into the front end of the washer. They enter a vestibule rinse that removes the bulk of the oil and aluminum fines from the cans. In many cases, this liquid goes directly to waste treatment. In other cases, built-in or 3rd party oil skimmers are used to separate the oils before disposal.
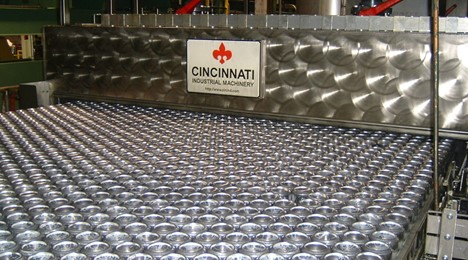
Pre-Wash:
After having their domes blown out, (which occurs after every spray stage) the cans enter a high-pressure pre-wash stage. This stage, as well as the Wash stage that follows, uses a parallel moving overhead can support “hold down” to allow these light aluminum bodies to be sprayed with a high-pressure aqueous solution.
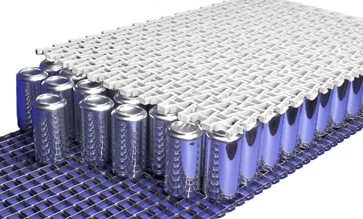
This stage uses a light concentration of chemicals with hot water to start the final cleaning process. More oils and aluminum fines are removed from the cans. In some cases, oil skimming is also used in this stage. To the extent that the oils can be removed from this tank, the chemicals will be more efficient.
Wash:
The cans then enter a high-pressure wash stage. This stage uses a highly concentrated chemical solution to do the final can cleaning, and to prepare the can surface.
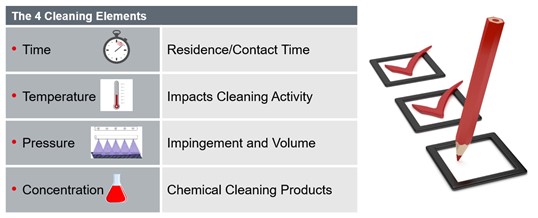
The common chemistry that is used in the wash stage includes a combination of sulfuric and hydrofluoric acids. Along with various surfactants, the sulfuric acid is used to clean the cans.
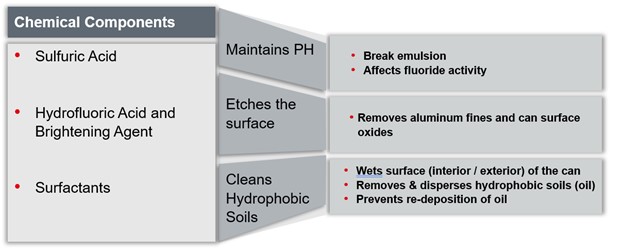
There is a fine balance in the use of the hydrofluoric acid (HF) in this stage. Too little HF results in the aluminum fines becoming a suspended solid versus being a dissolved solid. Keeping the aluminum dissolved is essential to keep these fines from making their way down the washer into the rinses.
Too much HF causes the can surface to go from a bright surface to a whitish surface. This “over etch” not only affects the reflectivity of the can, but it also makes the surface too rough to properly move through the line. Additionally, this white blush can be picked up on the decorator blankets, causing ink voids and any number of other problems.
Drag-out:
The cans then enter a short so called “drag-out” (or chemical knock off) stage. The idea is to “drag-out” the bulk of the acidified water that remains on the can as it leaves the Wash stage. This stage does a good job of reducing the chemical load that ends up in the following rinse stage. The liquid from this stage is the source of the spray in the Pre-rinse.
Rinse #1:
The can then enters a recirculating water rinse stage. The purpose here is very simple, that is to remove the remaining wash stage chemistry from the cans. This is done with low pressure ambient temperature water. Because this stage operates without the use of a “hold down” conveyer as used in the Pre-wash and Wash, can stability is an issue in this stage. Nozzle selection and nozzle alignment are an important consideration in this stage where there is a balance between rinsing power versus can stability.
Treatment:
The cans then enter a recirculating chemical stage. This stage is the treatment stage where the cans are given a conversion coating used to prevent brown staining of cans that go through a later retort process. The conversion coating also enhances the application of external decoration and internal spray coatings.
Rinse #2:
The cans then enter another recirculating water rinse stage. The purpose here again is to remove the remaining Treatment stage chemistry from the cans. This stage acts the same way as Rinse #1, except with a final spray of fresh water.
The fresh water that enters this stage is the source of water for the back flow system for the washer. A properly designed backflow system, where fresh water moves through various stages and exits at the Pre-Rinse is used to minimize the overall water consumption of the washer.
De-ionized Rinse:
The cans then enter a recirculating de-ionized water rinse stage. The purpose of this stage to give the cans a spot free rinse. The stage is configured in (2) phases.
The cans are first exposed to a recirculated de-ionized rinse where the water is a mix of fresh DI and recirculated DI, a so called “dirty DI” rinse.
The exit sprays of this stage are fed from the plant’s de-ionized system such that the cans are exposed to very pure water with virtually no dissolved solids. When dried, this pure water will result in a water spot-free can, essential when a “see through” can decoration is applied.
With some newer installations, RO water is used to provide the spot free final rinse.
Mobility Enhancer (ME):
The cans then enter an optional mobility enhancer stage. This optional stage applies a very light chemical coating that allows the can to move more easily through the conveyors on the can line. It has been found that can lines that run over 2,000 cans per minute can benefit from an ME stage.
Vacuum Transfer:
The cans are then conveyed from the washer to the dryer. Although a few can makers still use dead plates to transfer cans from the washer to the dryer, a vacuum transfer is a more popular option. The vacuum transfer has the advantage that it allows the few downed cans that develop in the washer to drop out and not be pushed into the dryer.
Dryer:
The purpose of the dryer is to dry off any moisture prior to the transfer to the decorator.
Unlike an inside bake oven, cure times are of no concern. All that is needed is to have the cans become “just dry” as they leave the dryer. High operating temperatures can cause the ME that was applied in the washer to be burned off, and extreme temperatures, (or long stoppages in the dryer), can result in a semi-annealing of the aluminum, leading to dome reversals when the can is under pressure. From an energy saving point of view, the goal is to operate the dryer at the lowest possible temperature in order to minimize operating expenses and energy use.
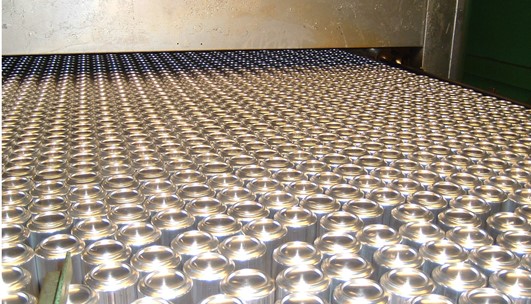
The operating temperature of the dryer is empirically determined and is affected by the residence time available, and the “water break” effect of the ME rinse.
Efficiency:
As with all equipment in a can line, improving operating efficiency is always under consideration.
Specifications for can washers often call for 99.95% throughout efficiency. That is, there is an allowance for only about 5 cans per 10,000 of spoilage.
In a Washer, spoilage is usually in the form of downed or tipped cans that fall out at the reject conveyor. Occasionally, dented, or scratched cans will appear, but an examination and correction of the can guides or hold down conveyor setting will eliminate this spoilage.
The more common form of spoilage is tipped cans that are a result of nozzle plugging or nozzle misalignment. Since these very lightweight cans must withstand rinsing with no means of support, a few partially plugged or misdirected nozzles can wreak havoc within a washer. Careful riser and nozzle maintenance on a down day is needed to minimize downed cans.
Washers are going “Green”:
Increasing concern about greenhouse gases, carbon footprint, as well as overall energy consumption have brought a focus on the reduction of energy of equipment in a can line.
The washer/dryer is a large piece of equipment where recent “Green” improvements have been made.
Some of the improvements are:
- Oil skimmers and oil removal systems to reduce water consumption. Washers now offer oil separators in various forms and with various levels of sophistication. Simple oil settling tanks can float out oils to reduce the load on the waste treatment system. More sophisticated oil separation units with pumps and holding tanks have reportedly been able to reduce the washer’s overall water consumption by 1/3.
- Non-acid wash stages. Alternate wash chemistries are being developed that eliminate the HF, resulting in simpler waste treatment and a more environmentally friendly washer.
- The use of RO water as a final rinse reduces the overall use of chemistry in the washing system.
- Operating pumps and blowers with variable frequencies drive to reduce energy costs when pump throttling and fan dampening is required.
- 6” thick insulated panels of the dryer are being used versus the 4” used in the past, with less heat released into the atmosphere.
- Washer tank insulation is used to reduce energy costs.
- Reduce dryer operating temperature in response to line speed. As the line speed varies, the dryer temperature modulates to just dry the can.
- The use of Kevlar dryer conveyors reduces energy consumption by dragging less heat out of the dryer compared to stainless steel belts.
- Vacuum belt strippers are used to reduce water and chemical consumption by minimizing the water and chemicals that are being carried on the belt from stage to stage.
The washer as part of a system:
The can washer/dryer looks like a standalone machine connected by conveyors to a can line, but it is an integral part of a beverage can line. As such, there are several pieces of support equipment that are involved with washer/dryer operation.

Some of these subsystems that washer manufacturers can supply are:
- Hot water heater to heat the tanks for plants that do not have or do not want to use plant generated steam
- De-ionizers to supply the required pure water to the final rinse of the washer. Optionally, RO systems provide this spot free water.
- Chemical control systems that can be integrated directly into the machine and it’s PLC
- Waste treatment for the washer
- Corrosion resistant platforms for any walkways
- Thermal energy recovery
As you can see, the evolution of the can washer has come a long way from the very beginning when lines crept along at 125 cans per minute. After nearly sixty years, can washing and drying has evolved along with the beverage and food can making industry. The can washer design has paralleled industry needs as well as political and social demands for a highly efficient, specialized and ecologically conscious system, capable of cleaning more than 6000 cans per minute.